Produserer 95 prosent av eget forbruk.
Ytterst i Fosen i Trøndelag, og med skipsleia rett utenfor, ligger Mowi Feeds fôrfabrikk. For en landeveisfarende kan det virke rimelig avsidesliggende. Men for selskapets bulkbåter som frakter laksens måltider langs norskekysten, er dette den perfekte beliggenhet.
Fabrikken i Bjugn stod ferdig sommeren 2014, og den gang var det hårete målet om å bli selvforsynt med fôr. Nå er det målet langt med vei nådd. Fabrikkene produserer 95 prosent av fôret Mowi-laksen konsumerer.
De 69 ferdigvaresiloene ved Valsneset kan fylles med 8.625 tonn. Kapasiteten her på 400.000 tonn fôr, og toppåret var i 2020 med 389.000 tonn produsert fôr. Selv om produksjonen i fjor var lavere, med nær 372.000 tonn, ble det det mest lønnsomme året for fôrprodusenten. Operasjonelt EBITDA ble 47 millioner euro.
Nøysom logistikk
Fabrikken i Kyleakin i Skottland ble åpnet i 2019. Der er den årlige kapasiteten på 240.000 tonn fiskefôr.
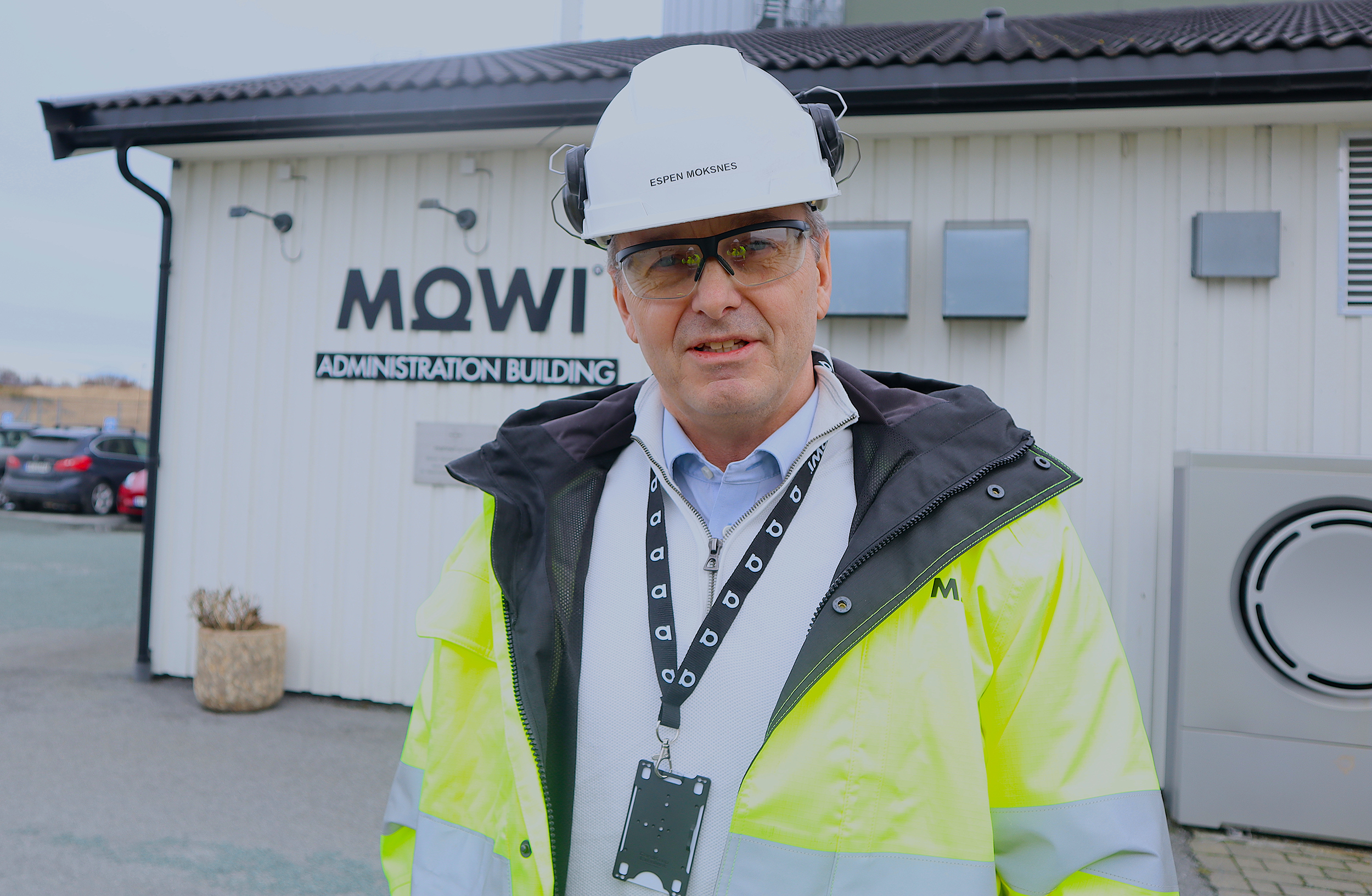
Espen Moksnes er selskapets logistikkdirektør, med ansvar for at alt fôr kommer ut til rett tid og anlegg over hele Europa.
– Volumet vi produserer er etter bestilling fra farming, så etterspørselen styrer produksjonen. At det ble såpass høyt i 2020, skyldes primært nyanser, sier Moksnes til iLaks. Han leder også planavdelingen, som sørger for at rett mengde råvarer kommer inn til fabrikken.
– Februar og mars er månedene med lavest produksjon. Høysesongen er på topp i juli, og den varer gjerne helt ut i oktober. Planavdelingen legger til grunn det som ligger inne av prognoser og ordre fra farming. Prognosene oppdateres gjerne flere ganger i måneden, sier Moksnes.
– Det vi produserer er primært til bulk, men av og til krever kunder eller logistikken det at det sendes ut en sekk eller to. Hvor mye de skal ha på sjøen eller ved båt varierer fra uke til uke. Vi har ikke et bestemt krav om hvor mye vi skal på lager av fôr, men vi opererer med en tommelfingerregel på minst én ukes forbruk på lager til enhver tid, sier Espen Moksnes.
I disse dager er lagrene på mer enn det, ettersom fabrikken skal gjennom full vedlikeholdsperiode. Det betyr at produksjonen stanses i to uker, før det er full aktivitet igjen før påskeuka.
Vindkraft og LNG
Espen Moksnes og Site Manager, Rune Jøssund-Valsø, viser iLaks rundt på det store anlegget. Industriområdet er et av flere i regionen som er regulert for vindkraft, så en nærmeste naboene er TrønderEnergis åtte vindmøller. Når møllene snurrer rundt for fullt, tar Mowi Feed unna det meste av strømmen derfra.
Ved siloene står tankene med LNG, som siden 2014 brukes på stimkjel og tørker inne i fabrikken. Men også bulkbåtene benytter LNG.
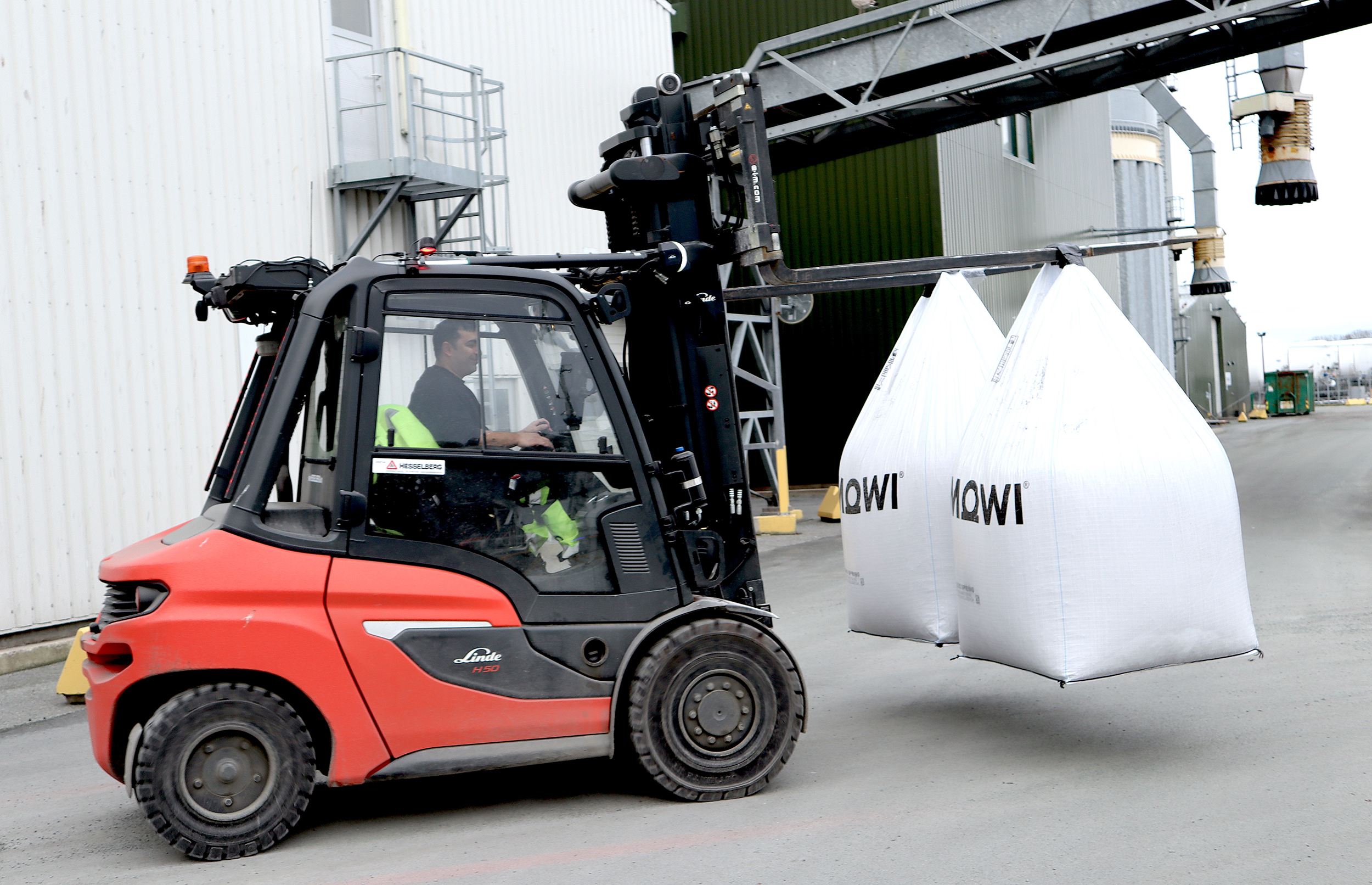
Utfra en av portene kommer en truck med to sekker hengene på gaffelen. De er på vei mot kaia, der en fraktebåt er klar til å ta imot 500 fôrsekker. Lasten skal fraktes til lageret i Karmøy.
De siste par ukene har staben på 67 vært i full gang med den årlige revisjonen. Men noe skal også gjøres for aller første gang.
– Fokuset nå er å revidere alt av utsyr og maskiner. Alt skal holde i et helt nytt driftsår. Gjennom året er det kun mindre stopp hver tredje uke, der vedlikeholdsteamet har fem timer på seg, sier Jøssund-Valsø.
Når det er to uker med full stopp, trår alle i produksjonen til. I tillegg kommer en rekke representanter fra de som leverer utstyr og maskiner for å bistå.
– Alt skal legges til rette for at dette skal driftes i ett år til, og det skal skje uten driftsforstyrrelser, slår Jøssund-Valsø fast.
Byttes for første gang
Alle maskiner i fabrikken åpnes, sjekkes og gjøres klar i løpet av et par hektiske uker. Utenfor er det særlig to oppgaver Jøssund-Valsø er spent på, én av dem er det som skal skje med biofilteret.
– Alt av prosessluft passerer dette filteret. Innholdet, biofilter meda, skal byttes ut for første gang. Hele 40 lastebiler kreves det for å fylle alt med nytt innhold. Dette er en stor jobb som vi gjør kanskje bare hvert tiende år. Den største utfordringen er at alt må skje i løpet av en produksjonsstopp på få dager, forklarer han.
Ut fra fabrikken går to transportlinjer, som hver kan frakte 300 tonn i timen (t/h) med ferdigvare ut, og en linje med samme kapasitet for tørre råvarer inn.
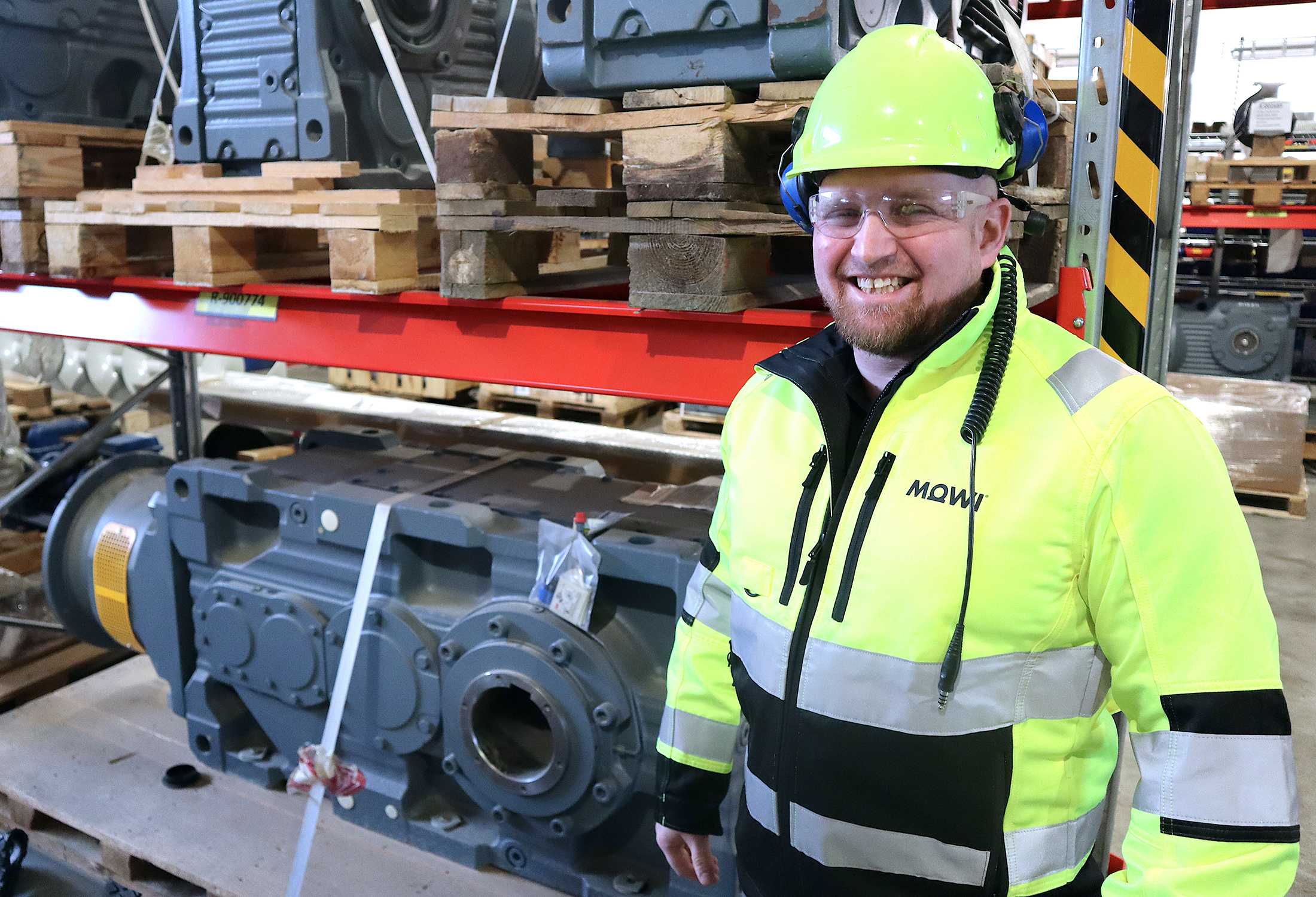
– På den ene ferdigvarelinjen skal en conveyor byttet ut grunnet slitasje, sier Jøssund-Valsø, og viser vei inn i utstyrslageret. Her er alt plassert i et sirlig system, merket med tall og fargekoder som viser utstyret status og hvor det hører hjemme. Utstyr som er kritisk for produksjonen skal det til enhver tid være to av. Gearet er trolig det som er mest kritisk.
– Dette gearet er det største som finnes på fabrikken. Bestillingstiden for et nytt er halvannet år. Om det som er i bruk havarerer blir det krise. Derfor må vi ha ett stående klart hele tiden. Gearet må sendes til Sverige for overhaling, ingen i Norge tar denne størrelsen, smiler Jøssund-Valsø.
Små grep hele veien
I fabrikken er det to produksjonslinjer, som ble tatt i bruk samtidig da åpnet i 2014. Siden den gang har staben drevet frem en rekke forbedringer av maskineriet. Noen ombygginger har det også blitt gjort, forteller han.
– Det er små grep vi har gjort hele veien. Det har ført til at vi har kunnet øke kapasiteten og forbedret effektiviteten hele veien. Det kan være plassering av råvarer, utstyr og andre forbedringer som kan øke produksjonen per time.
– Når det gjelder utstyr, er det ikke større planer om endringer fremover. Men innenfor arbeidsmetodikk og mulige flaskehalser i arbeidsprosessene vi ser muligheter. Når vi har vokst så raskt som vi har gjort, må vi stoppe opp litt for å komme ajour og få alt på plass, sier Rune Jøssund-Valsø.
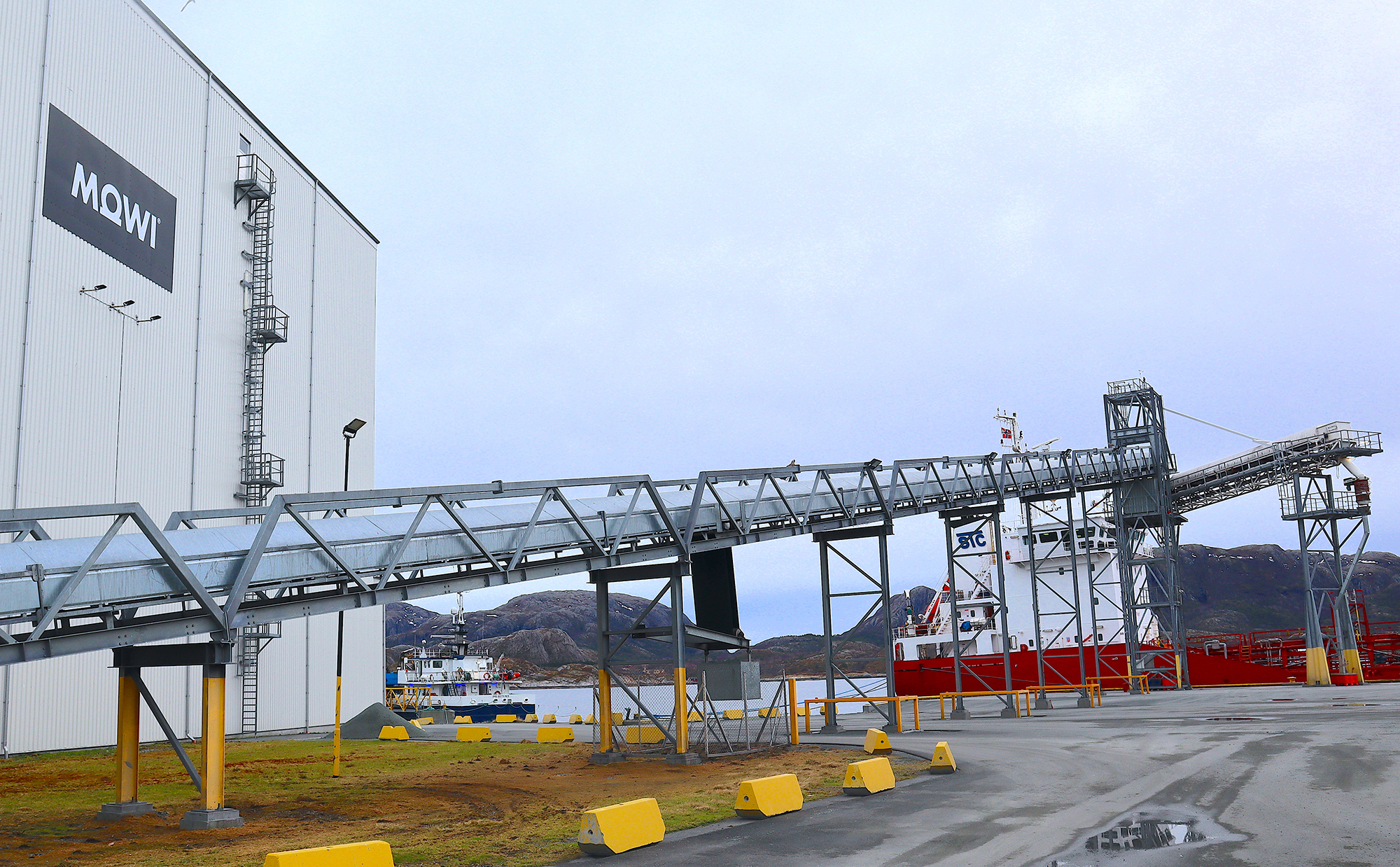